CE for BESS: Complete Guide to Battery Energy Storage Certification
Why CE for BESS Matters? Battery Energy Storage Systems (BESS) are rapidly expanding across the globe. As renewable energy grows, the need for safe, reliable, and compliant storage solutions becomes critical.
CE for BESS plays a central role in ensuring that energy storage systems meet essential safety, health, and environmental standards in Europe. However, CE certification is only part of the larger compliance picture.
This article explains what CE means for BESS, what it covers, why many companies prioritize CE, and why additional certifications like UL and IEC are essential.
What Does CE Certification Mean for BESS?
The CE mark (Conformité Européenne) is a mandatory certification for products entering the European Economic Area (EEA). For BESS, CE shows compliance with EU directives and harmonized standards.
When a BESS carries the CE mark, it declares conformity with the following directives:
- Low Voltage Directive (LVD) – Protects against electrical hazards.
- Electromagnetic Compatibility (EMC) Directive – Prevents electrical interference.
- Restriction of Hazardous Substances (RoHS) – Limits toxic chemicals in batteries and components.
- General Safety Directives – Cover risks related to machinery and consumer use.
In essence, CE for BESS confirms that the system has met basic EU safety and environmental requirements, allowing it to be legally marketed and installed in Europe.
What Does CE for BESS Cover?
CE certification for BESS evaluates multiple aspects of product safety. These include:
- Electrical Safety – Preventing risks of electric shock, short circuits, and overheating.
- Thermal Safety – Assessing insulation, cooling design, and fire prevention.
- Electromagnetic Compatibility (EMC) – Ensuring the BESS does not emit disruptive signals.
- Environmental Safety – Controlling hazardous substances and ensuring recyclability.
However, CE certification for BESS is primarily based on a self-declaration of conformity. Manufacturers test the product internally or through a notified body, then issue a Declaration of Conformity (DoC).
This process makes CE less complex compared to third-party certifications like UL or IEC, which require independent validation and rigorous lab testing.
Why Do Most Companies Choose Only CE Certification for BESS?
Many BESS companies stop at CE certification instead of pursuing more demanding approvals. The main reasons include:
- Lower Costs: CE testing is more affordable than UL or full IEC certification, which involve expensive third-party audits.
- Faster Market Entry: CE certification is quicker, often taking weeks instead of months.
- Simpler Process: CE allows self-declaration, reducing reliance on external labs.
- Minimum Requirement: Since CE is mandatory in the EU, many companies view it as the lowest barrier to entry.
In other words, CE is often seen as the easiest, fastest, and cheapest way to access the European market. But relying on CE alone raises important safety concerns.
Is CE Alone Enough for BESS Safety?
The answer is no. While CE for BESS ensures legal entry into the EU market, it does not fully address the complex safety risks of modern energy storage systems.
BESS involves large-scale lithium-ion batteries, which can pose hazards like:
- Thermal Runaway – Fire and explosion risk if cells fail.
- High Voltage Risk – Danger of electric shock during installation or maintenance.
- System-Level Failure – Risks from inverters, converters, or control systems.
To mitigate these risks, global safety standards go far beyond CE. Manufacturers often need UL, IEC, or national certifications depending on their target markets.
Key International Standards Beyond CE
Here are the most important certifications that complement CE for BESS:
1. IEC Standards (International)
- IEC 62619: Safety requirements for lithium-ion batteries used in stationary storage.
- IEC 62933 series: Covers energy storage integration into power grids.
- IEC 62109: Focuses on safety of power converters.
2. UL Standards (North America)
- UL 9540: Safety requirements for complete BESS systems.
- UL 1973: Safety of battery modules for stationary applications.
- UL 9540A: Test method for thermal runaway fire propagation.
3. National Certifications
- BIS (India): Mandatory for lithium-ion cells and BESS units.
- TISI (Thailand): Battery certification for safety and performance.
- KC (Korea): Compliance for batteries and power systems.
- PSE (Japan): Electrical safety approval.
Together, these standards ensure that a BESS is safe, grid-compatible, and globally marketable.
CE vs UL vs IEC: Key Differences
Certification | Region | Scope | Testing Requirement | Market Perception |
---|---|---|---|---|
CE | Europe | Basic health, safety, EMC | Self-declaration or notified body | Entry-level compliance |
UL 9540 | USA/Canada | Full system safety | Third-party lab required | High credibility |
IEC 62619 / 62933 | Global | Battery + system safety | Third-party testing | Widely respected |
BIS / KC / PSE | National | Country-specific safety laws | Mandatory local tests | Legal requirement |
This table shows why CE is the easiest to achieve but IEC and UL carry higher safety credibility.
Why BESS Needs Multiple Certifications
Unlike small electronics, BESS operates at industrial-scale energy levels, which makes multi-layer certification essential.

- CE ensures compliance in Europe, but it does not evaluate system-level fire safety.
- UL validates complete system safety and is trusted in North America.
- IEC sets a global benchmark, especially for grid integration.
- National standards guarantee local approval, allowing sales in markets like India, Japan, or Korea.
Therefore, CE should be seen as the foundation, while UL, IEC, and national approvals are the reinforcements. Together, they create a safe and credible BESS product.
Why Companies Should Go Beyond CE
Although CE is attractive for cost and speed, relying on it alone can lead to challenges:
- Limited Market Reach: CE only works in Europe, not globally.
- Lower Buyer Confidence: Utilities and large clients often demand UL or IEC reports.
- Safety Risks: CE’s self-declaration model may overlook thermal runaway or fire propagation risks.
- Regulatory Pressure: More countries are adopting stricter BESS safety laws.
Companies that invest in full certification portfolios gain stronger market access, brand reputation, and customer trust.
Conclusion: CE is Essential but Not the Final Step
CE for BESS is a mandatory starting point for European market access. It ensures compliance with basic safety, EMC, and environmental standards. However, CE is not enough to prove the full safety of complex battery energy storage systems.
Most companies choose CE because it is fast, affordable, and easy, but long-term success requires additional certifications like UL 9540, IEC 62619, and BIS. These provide independent validation, global acceptance, and higher safety assurance.
In the evolving energy landscape, BESS manufacturers and project developers must go beyond CE certification to build trust, reliability, and international growth opportunities.
Understanding the Economics of C&I BESS Deployment
C&I BESS economics is becoming a critical consideration for businesses investing in energy storage solutions. By evaluating costs, return on investment (ROI), and key applications such as peak shaving, energy shifting, and renewable integration, companies can strategically plan how battery energy storage systems (BESS) deliver long-term financial and operational benefits.
Why C&I BESS Economics Matters
The adoption of commercial and industrial battery energy storage systems is no longer just about sustainability. It’s about cost competitiveness, business continuity, and energy independence. C&I BESS helps organizations reduce energy expenses, optimize renewable energy use, and avoid downtime caused by grid instability.
For decision-makers, the economics provide the blueprint for determining whether a system is financially viable. Unlike traditional infrastructure, BESS generates multiple revenue streams—making it a compelling long-term investment.
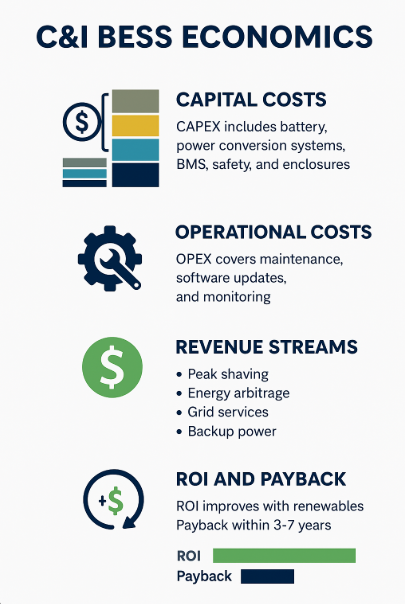
Cost Components of C&I BESS
When evaluating C&I BESS economics, businesses need to consider all the cost components involved in deployment:
- Capital Expenditure (CAPEX): Includes the cost of battery modules, power conversion systems (PCS), enclosures, and installation.
- Operational Expenditure (OPEX): Covers routine maintenance, software updates, and monitoring systems.
- Integration Costs: Grid interconnection, compliance with utility standards, and renewable energy integration.
- Safety & Compliance Costs: Fire safety systems, IP-rated enclosures, and certifications to meet international standards.
Understanding these costs ensures businesses can budget accurately and anticipate ROI timelines.
Return on Investment (ROI) for C&I BESS
ROI is one of the most attractive elements of C&I BESS economics. While upfront costs may seem high, the savings and revenue opportunities deliver significant returns. Key ROI drivers include:
- Energy Bill Savings: Demand charge reduction and peak shaving lower operational expenses.
- Grid Services Revenue: Businesses can participate in frequency regulation and demand response programs.
- Enhanced Renewable Utilization: Solar and wind power can be stored and used later, reducing reliance on expensive grid power.
- Backup Power Value: Avoiding downtime and protecting operations ensures business continuity.
Typically, ROI periods range from 3–7 years, depending on system size, energy pricing, and incentive availability.
Peak Shaving: A Core Economic Benefit
One of the strongest links in C&I BESS economics is peak shaving. Utilities often charge businesses based on their highest 15-minute demand interval each month. By deploying stored energy during peak demand, companies reduce these costly charges significantly.
👉 Read more about C&I BESS applications for peak shaving here.
Applications Driving C&I BESS Economics
Beyond peak shaving, several applications contribute to positive BESS economics:
- Energy Shifting: Storing cheap off-peak power for use during high-tariff hours.
- Microgrid Support: Ensuring resilience and independence from grid instability.
- EV Charging Integration: Supporting electric vehicle fleet charging without overwhelming the grid.
- Renewable Energy Optimization: Aligning variable renewable supply with steady industrial demand.
👉 Explore the full range of C&I BESS applications here.
Incentives and Policy Support
C&I BESS economics improve dramatically when businesses leverage incentives and policy support. Many governments and utilities offer:
- Tax Credits & Subsidies for renewable-linked storage projects.
- Utility Rebates for demand reduction.
- Green Financing Options that lower CAPEX burden.
These programs shorten the payback period and strengthen the investment case.
Barriers to Strong Economics
Despite the benefits, certain challenges affect C&I BESS economics:
- High Upfront CAPEX compared to traditional energy solutions.
- Uncertain Energy Tariffs that impact ROI predictability.
- Complex Regulatory Approvals for grid-connected projects.
- Technology Risks tied to battery degradation over time.
However, with falling battery costs and stronger policy frameworks, these barriers are steadily declining.
The Long-Term Value of C&I BESS
The true value of C&I BESS economics goes beyond immediate savings. Businesses gain:
- Energy Cost Stability: Protection against volatile energy prices.
- Sustainability Branding: Meeting ESG and decarbonization goals.
- Future-Readiness: Supporting electrification and digital operations.
In a competitive global market, companies that adopt BESS early gain a strong operational and reputational edge.
Conclusion
C&I BESS economics proves that energy storage is not just a cost—it’s a strategic investment. From peak shaving to renewable integration, the financial and operational benefits outweigh the challenges. With the right planning, incentives, and applications, commercial and industrial energy storage transforms from an expense into a long-term value generator.
By understanding these economics, businesses can make informed decisions, optimize their energy strategies, and strengthen both resilience and profitability in a rapidly evolving energy landscape.
How C&I BESS Enhances Solar and Wind Power Integration
As renewable energy adoption accelerates, businesses are investing in solar and wind power to reduce costs, cut emissions, and achieve sustainability goals. However, the challenge of intermittency—the variability of renewable energy output—remains a barrier to full reliability. This is where C&I BESS with renewable energy plays a transformative role. By providing storage, flexibility, and stability, Battery Energy Storage Systems (BESS) enable companies to maximize the value of their renewable assets.
The Intermittency Challenge in Renewable Energy
Solar and wind energy are inherently variable. Cloud cover can reduce solar production within minutes, while wind speed changes affect turbine output. Without a buffer, these fluctuations can lead to instability, grid imbalances, or even curtailment of renewable energy. For businesses that rely on consistent power for manufacturing, data centers, or logistics, unpredictability becomes a costly problem.
C&I BESS with renewable energy addresses this issue by storing excess electricity when generation is high and releasing it when demand spikes or output drops. This ensures steady energy delivery, even when renewable sources fluctuate.
Energy Shifting: Maximizing Renewable Value
One of the greatest advantages of BESS is energy shifting. With storage in place, businesses can:
- Capture solar energy during peak sunlight hours and use it in the evening when demand and grid prices are higher.
- Store wind power generated overnight and release it during working hours.
- Reduce dependency on expensive peak-hour electricity.
By shifting energy use, C&I BESS with renewable energy ensures companies optimize both their operational costs and sustainability performance.
Supporting Microgrids for Energy Independence
Another growing trend is the deployment of microgrids, where localized power networks combine renewable generation, storage, and sometimes backup generators.
C&I BESS enhances microgrids by:
- Providing islanded operation during grid outages, keeping facilities powered.
- Enabling seamless integration of solar panels, wind turbines, and other distributed resources.
- Balancing local supply and demand in real time.
For businesses operating in remote areas or regions with unstable grids, C&I BESS with renewable energy makes energy independence achievable.
Grid Services and Demand Response
Beyond internal use, BESS enables companies to participate in grid programs. By integrating renewable assets with storage, businesses can:
- Offer demand response, reducing load during peak events.
- Provide frequency regulation by discharging or absorbing energy instantly.
- Contribute to grid stability while generating new revenue streams.
This dual role—supporting both business operations and the wider grid—demonstrates the strategic advantage of pairing C&I BESS with renewable energy.
Real-World Applications
Several industries are already leveraging this synergy:
- Manufacturing plants integrate solar with BESS to avoid downtime and reduce peak energy costs.
- Cold storage facilities use wind plus storage to stabilize refrigeration loads.
- Campuses and hospitals adopt renewable-powered microgrids with BESS to ensure uninterrupted operations during outages.
These examples highlight how C&I BESS with renewable energy is not just a trend—it’s becoming a business necessity.
Sustainability and Corporate Goals
Today, corporations are under increasing pressure to achieve net-zero emissions. By combining renewable generation with energy storage, businesses can:
- Maximize renewable utilization rates.
- Reduce reliance on fossil-fuel-based backup systems.
- Meet Environmental, Social, and Governance (ESG) reporting requirements.
In this way, C&I BESS with renewable energy contributes not only to cost savings but also to long-term brand reputation and compliance with global sustainability frameworks.
Conclusion
The integration of C&I BESS with renewable energy is revolutionizing how businesses harness solar and wind power. By reducing intermittency, enabling energy shifting, supporting microgrids, and providing grid services, BESS empowers companies to take full advantage of renewable investments. For forward-looking enterprises, storage is no longer optional—it is essential to building a reliable, resilient, and sustainable energy future.
IEC 62933: Global Standard for Grid Energy Storage Systems
As renewable energy adoption grows, energy storage systems (ESS) have become critical for balancing supply and demand, improving reliability, and supporting grid resilience. To ensure safety, performance, and interoperability, the International Electrotechnical Commission (IEC) developed the IEC 62933 series, a set of globally recognized standards.
These standards guide manufacturers, developers, and policymakers in designing and deploying safe, efficient, and sustainable storage solutions.
What is IEC 62933?
The IEC 62933 series establishes a framework for electrical energy storage (EES) systems, including grid-scale and commercial applications. It covers general requirements, safety, performance, environmental considerations, and grid integration.
Rather than being a single document, IEC62933 is a family of interlinked standards, each addressing a specific aspect of EES.
Breakdown of Key IEC 62933 Standards

Here’s a detailed overview of the most important parts:
1. IEC 62933-1 – General Requirements
- Defines basic concepts, classifications, and terminology for EES.
- Provides common ground for stakeholders (manufacturers, regulators, utilities).
- Establishes a systematic approach to planning, designing, and evaluating ESS.
2. IEC 62933-2-1 – Performance Testing for EES Systems
- Sets methods to evaluate performance of storage systems.
- Covers energy efficiency, response time, storage capacity, and life cycle.
- Ensures consistent benchmarks for comparing technologies.
3. IEC TS 62933-2-2 – Functional Safety Assessment
- A Technical Specification (TS) focusing on safety from a system function perspective.
- Addresses potential hazards (thermal runaway, electrical failures).
- Provides methods for risk identification and mitigation.
4. IEC TS 62933-2-3 – Reliability of Energy Storage Systems
- Defines testing and assessment methods for reliability.
- Covers failure rates, durability, and long-term system resilience.
- Helps ensure stable operation in grid-critical applications.
5. IEC TR 62933-2-201 – Guidance on Safety Cases
- A Technical Report (TR) providing practical guidance for ESS safety cases.
- Supports developers and operators in building safety documentation.
- Bridges the gap between technical standards and real-world applications.
6. IEC 62933-4-2 – Environmental Impact of EES Systems
- Focuses on environmental assessment of energy storage technologies.
- Considers carbon footprint, material use, and recycling practices.
- Encourages sustainable deployment of large-scale ESS.
7. IEC 62933-4-4 – End-of-Life Management
- Provides guidelines for decommissioning, recycling, and disposal of EES.
- Promotes circular economy practices in the storage industry.
- Reduces environmental risks associated with battery waste.
8. IEC 62933-5-1 – General Safety Considerations
- Covers general safety requirements for stationary energy storage.
- Includes electrical, chemical, mechanical, and fire safety aspects.
- Ensures system safety across all technologies (batteries, flywheels, etc.).
9. IEC 62933-5-2 – Safety for Large-Scale EES
- Focuses specifically on large battery energy storage systems (BESS).
- Addresses thermal runaway prevention, emergency response, and system protection.
- Critical for utility-scale storage projects.
10. IEC 62933-5-3 – Grid Integration Safety
- Examines safety aspects during grid connection and operation.
- Ensures ESS does not destabilize or endanger grid infrastructure.
- Supports secure deployment in smart grids and microgrids.
Importance of IEC 62933 for the Industry
The IEC 62933 series provides:
- Global Standardization – unifies practices worldwide.
- Risk Reduction – prevents failures in high-risk ESS installations.
- Sustainability – ensures safe end-of-life handling.
- Investor Confidence – promotes compliance and long-term reliability.
- Innovation Support – enables safe integration of emerging technologies like solid-state and hybrid storage.
Conclusion
The IEC62933 standard family is the backbone of global energy storage deployment. From general guidelines (IEC62933-1) to detailed safety (IEC62933-5-2) and environmental sustainability (IEC62933-4-4), it ensures storage systems are safe, efficient, and future-ready.
Adopting these standards is essential for manufacturers, developers, and regulators who aim to accelerate the clean energy transition while ensuring safety and reliability.
C&I BESS Safety Standards: Ensuring Reliability, Compliance, and Protection
C&I BESS Safety Standards: Commercial and Industrial Battery Energy Storage Systems (C&I BESS) are becoming indispensable for businesses looking to reduce costs, enhance resilience, and integrate renewable energy. Yet, the growth of these systems comes with a critical requirement: safety.
Without robust safety measures, risks such as fire incidents, electrical faults, or environmental hazards could undermine the very benefits C&I BESS offers. This is where C&I BESS Safety Standards come into play. They provide the guidelines and certifications that ensure every component — from battery modules to enclosures — operates safely and reliably under demanding conditions.
In this post, we’ll explore the key safety standards for C&I BESS, including fire safety protocols, IP-rated enclosures, testing procedures, and compliance frameworks.
1. Battery Safety: The Foundation of Protection
The battery modules are the heart of every C&I BESS. Most systems today use lithium-ion technology, which offers high efficiency and long cycle life but requires strict adherence to safety protocols.
Key Safety Standards for Batteries:
- UL 1973: Governs battery systems for stationary and motive applications, ensuring safe design and performance.
- IEC 62619: International standard for rechargeable lithium batteries used in industrial applications.
- Thermal Runaway Protection: Advanced designs integrate shutdown separators, flame-retardant electrolytes, and pressure relief valves to minimize risks.
By meeting these battery safety standards, C&I BESS providers can prevent catastrophic failures and improve system reliability.
2. Fire Safety Measures: Preventing and Containing Hazards
One of the most discussed topics in C&I BESS Safety Standards is fire protection. Given the energy density of modern batteries, the risk of overheating or thermal runaway is real — and prevention is critical.
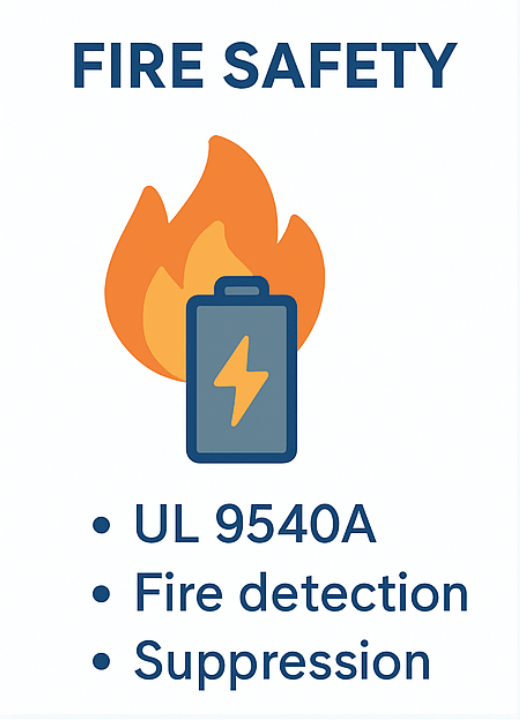
Fire Safety Practices in C&I BESS:
- UL 9540A Test: Evaluates fire propagation risk in battery systems.
- Automatic Fire Suppression: Systems often use clean agent gases (like Novec 1230) or water mist technologies.
- Fire Detection Sensors: Smoke and gas detectors installed inside enclosures ensure early warning.
- Emergency Venting: Proper ventilation prevents gas buildup during overheating events.
With these safeguards, facilities can minimize the risk of fire spreading and protect both infrastructure and personnel.
3. IP-Rated Enclosures: Shielding Against Environment
Environmental protection is another core aspect of C&I BESS Safety Standards. Since many C&I systems are installed outdoors, they must withstand dust, water, and harsh weather.
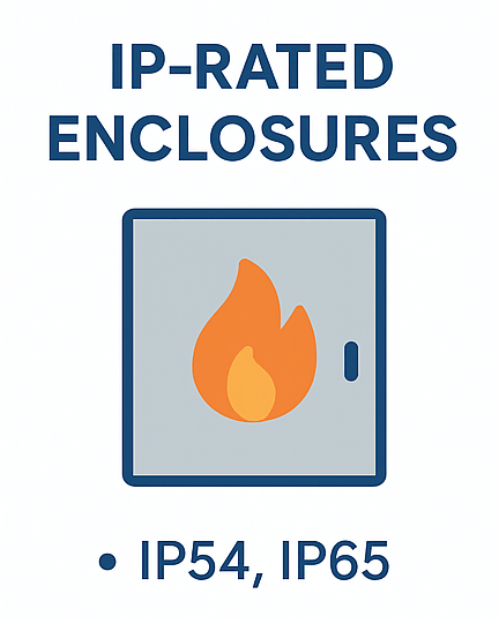
Common IP Ratings for C&I BESS:
- IP54: Protects against limited dust ingress and water spray.
- IP65: Dust-tight and protected against water jets.
- IP67: Offers full dust protection and resistance to temporary immersion.
A properly rated enclosure ensures batteries and electronics remain safe from external hazards, extending system life and reducing failure risks.
4. Electrical Protection and Circuit Breakers
Electrical faults are another potential hazard in BESS installations. To meet C&I BESS Safety Standards, robust electrical protections must be integrated.
Key Components:
- Circuit Breakers and Fuses: Prevent damage from overcurrent and short circuits.
- Surge Protection Devices (SPD): Safeguard equipment from voltage spikes caused by lightning or grid disturbances.
- Grounding and Isolation: Ensure personnel safety and fault clearance.
These protections create multiple layers of safety, ensuring both the equipment and people remain secure.
5. Thermal Management Systems
Maintaining the right temperature is essential for battery safety. Overheating accelerates degradation and raises fire risks, while extreme cold reduces performance.
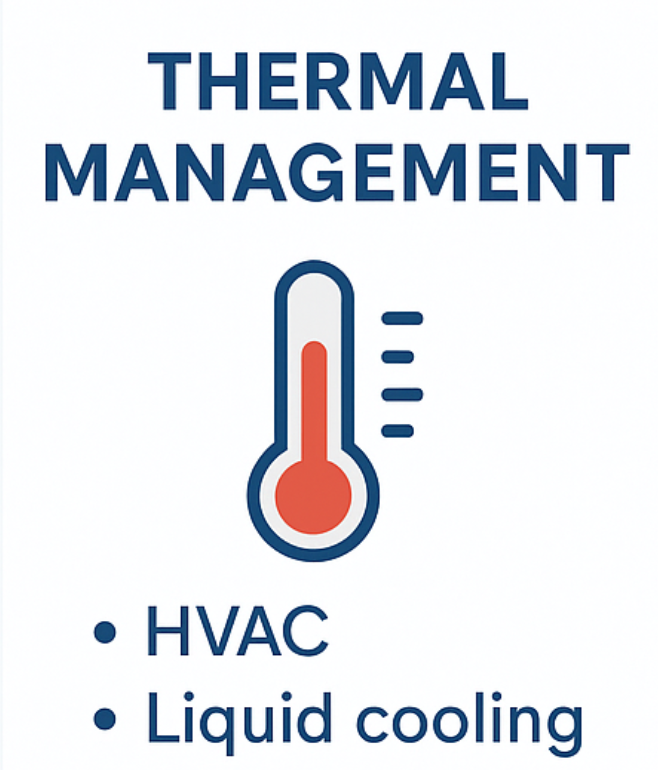
Thermal Management Standards:
- HVAC Integration: Ensures optimal airflow and cooling.
- Liquid Cooling Systems: Offer higher efficiency for large-scale C&I BESS.
- Temperature Monitoring: Real-time sensors alert operators to abnormal heat levels.
Complying with these thermal management protocols ensures safe operation across varying climates and load profiles.
6. Monitoring, EMS, and Communication
The Energy Management System (EMS) plays a crucial role in meeting C&I BESS Safety Standards. Beyond optimizing performance, it ensures early detection of anomalies.
Safety Functions of EMS:
- State-of-Charge Management: Prevents overcharging and deep discharging.
- Remote Monitoring: Enables 24/7 visibility of system health.
- AI-based Fault Detection: Modern EMS platforms use predictive analytics to anticipate failures.
When integrated with communication protocols, EMS ensures smooth interaction with the grid while maintaining safety compliance.
7. Compliance and Certifications
To build trust and ensure safe operation, C&I BESS solutions must comply with international and regional certifications.
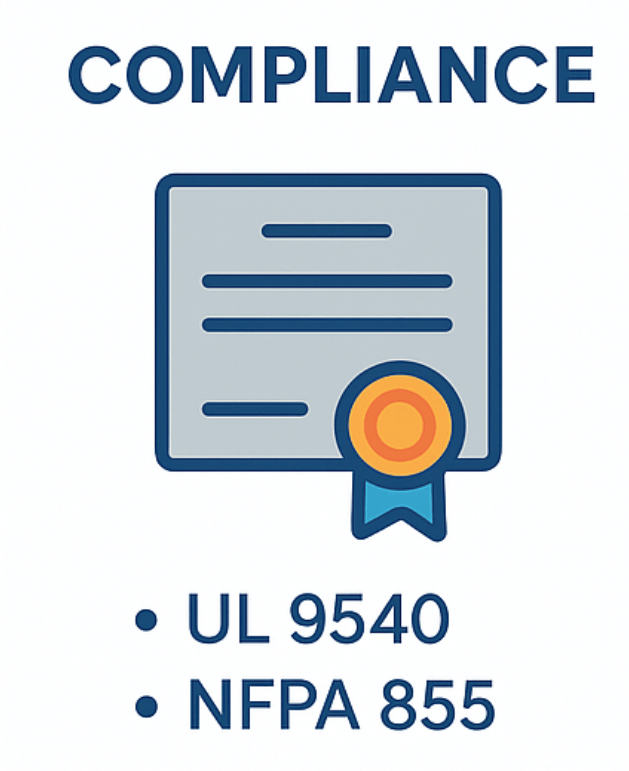
Key Certifications:
- UL 9540: Overall safety standard for energy storage systems.
- IEC 62933: Safety and performance requirements for grid-connected storage.
- NFPA 855: Fire protection standards specific to stationary energy storage installations.
Compliance with these certifications not only ensures safety but also makes projects easier to finance, insure, and operate.
Conclusion: Building Trust with Safety First
The success of energy storage in the C&I sector depends not only on performance but also on trust and safety. By adhering to strict C&I BESS Safety Standards — covering batteries, fire safety, IP-rated enclosures, electrical protections, thermal management, and compliance — businesses can deploy storage systems that are both reliable and secure.
As demand for clean energy grows, these standards will remain the backbone of safe innovation, ensuring that C&I BESS continues to empower industries without compromising protection.
Key Benefits of C&I Battery Energy Storage Systems (C&I BESS) for Enterprises
C&I BESS Benefits: The adoption of Commercial & Industrial Battery Energy Storage Systems (C&I BESS) is accelerating as businesses seek smarter energy solutions. While the technology itself is impressive, the real value lies in the benefits it brings to organizations.
From lowering energy bills to improving power resilience and supporting sustainability goals, a C&I BESS is more than just a storage system—it’s a business enabler. Let’s explore the key benefits that make C&I BESS essential for modern enterprises.
1. C&I BESS Benefits: Significant Cost Savings
One of the biggest benefits of C&I BESS is reducing energy costs. With applications such as peak shaving and load shifting, businesses can:
- Avoid high demand charges
- Buy energy at off-peak rates
- Optimize usage during expensive periods
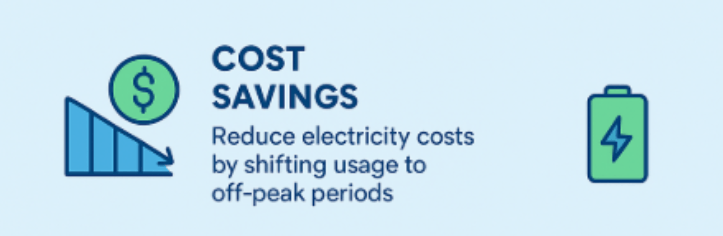
These savings can quickly add up, delivering a strong return on investment for businesses of all sizes.
2. C&I BESS Benefits: Energy Resilience and Reliability
For industries where downtime is not an option, a C&I BESS provides uninterrupted power supply during outages. Unlike traditional generators, BESS systems deliver instant backup without noise or emissions.
This benefit is particularly critical for:
- Manufacturing plants
- Data centers
- Healthcare facilities
- Logistics hubs
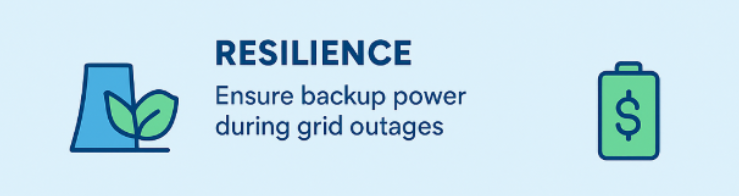
With a C&I BESS, businesses gain confidence in maintaining smooth operations even when the grid is unstable.
3. C&I BESS Benefits: Sustainability and Carbon Reduction
C&I BESS is a key driver of sustainability. By storing energy from renewable sources like solar or wind, businesses reduce reliance on fossil fuels and cut carbon emissions.
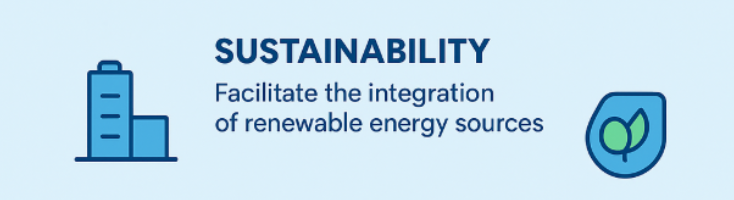
This not only improves environmental impact but also strengthens corporate ESG (Environmental, Social, and Governance) performance, which is increasingly important to investors and customers.
4. Revenue Opportunities
Beyond savings, a C&I BESS can generate new revenue streams. Through demand response programs, businesses can supply energy back to the grid during peak times and earn incentives from utilities.
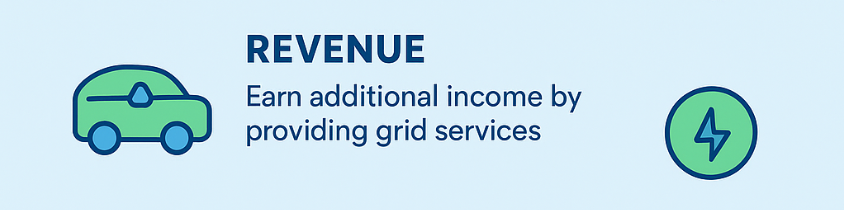
This transforms the C&I BESS into an active energy asset that contributes to financial growth.
5. Scalability and Flexibility
A major benefit of C&I BESS is its scalability. Systems can be tailored to fit specific needs, whether for small commercial operations or large-scale industrial facilities.
As energy demands grow, additional capacity can be added, ensuring businesses always have a solution that adapts to their needs.
6. C&I BESS Benefits: Support for EV Charging Infrastructure
With the rise of electric vehicles, businesses are increasingly installing charging stations. A C&I BESS helps manage charging loads by reducing strain on the grid and lowering infrastructure costs.
This benefit makes C&I BESS especially valuable for fleet operators, transport companies, and commercial charging hubs.
7. Enhanced Grid Participation
C&I BESS benefits extend beyond the facility itself. By supporting grid stability functions such as frequency regulation and voltage control, businesses contribute to a stronger, more reliable energy network.
This not only benefits utilities but also enhances the reputation of the business as a proactive energy leader.
Conclusion
The benefits of a C&I BESS go far beyond storage. From cost savings and resilience to sustainability, scalability, and new revenue opportunities, these systems offer long-term value to businesses across industries.
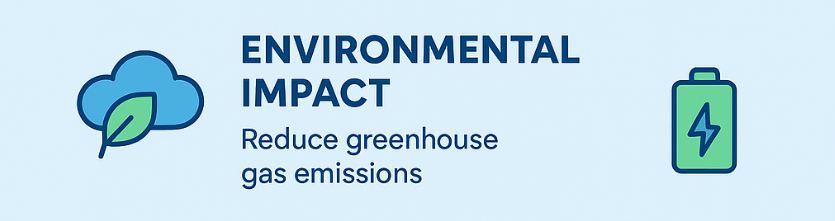
As energy demands grow and sustainability targets tighten, investing in a C&I BESS is not just a strategic decision—it’s a competitive advantage.
👉 Curious about real-world uses? Explore the Top Applications of C&I BESS to see how businesses are already leveraging these benefits.